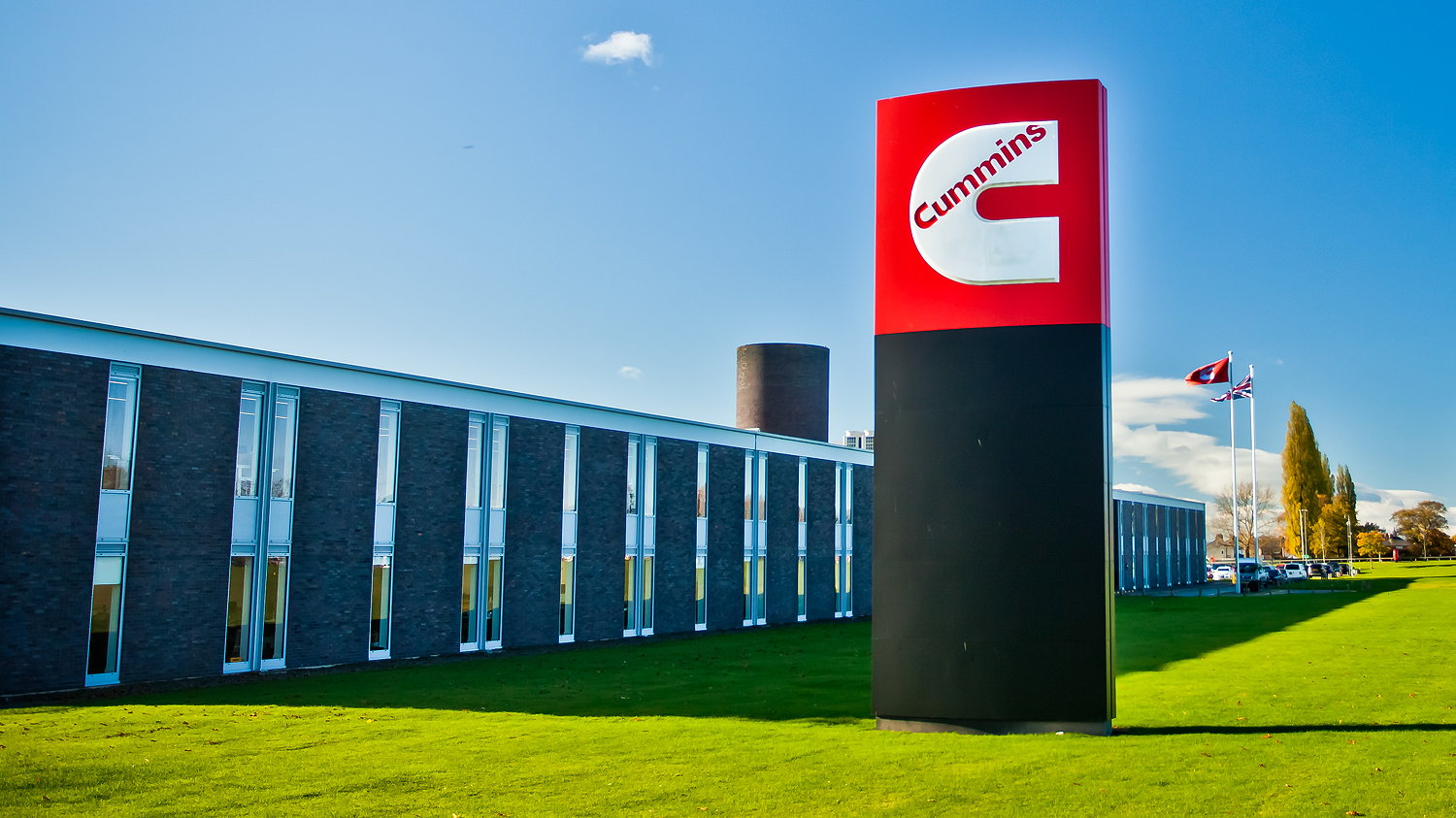
Cummins has announced it will open a new Powertrain Test Facility at its Darlington, UK campus to help accelerate the move towards cleaner, next-generation power technologies focused on reducing greenhouse gas emissions and improving air quality. The first phase of the £14 million investment is expected to open for operations by May 2023.
The facility is designed to be fuel-agnostic and will enable Cummins to develop and test a wider range of power technologies, including the latest universal engine platforms with variants able to operate on green hydrogen, renewable natural gas or sustainable diesel. Installation and testing capability will also extend to hydrogen fuel cell and battery electric powertrains.
Highly advanced dynamometers will be able to test not only powertrains, but also chassis-installed powertrains and vehicles, extending in size from a compact SUV to heavy-trucks of more than 44t or a double-deck bus. Off-road equipment, including construction machines and agricultural tractors, will also be able to be dyno-tested.
“We’re very excited to announce this significant investment in the new Powertrain Test Facility at Darlington, which will be an important element in Cummins Destination Zero strategy to deliver a broad portfolio of power solutions to meet the world’s sustainability challenges,” the executive director of Cummins on-highway business in Europe, Jonathan Atkinson, said.
“The new facility will further enhance the ability of Cummins European Technical Operations to introduce low-to-zero carbon power solutions and meet the forthcoming Euro VII very low emission regulations, likely to take effect around 2025.”
Covering a 738 square metre footprint, the two-story Powertrain Test Facility will significantly increase testing capacity with state-of-the-art capabilities at Cummins’ Darlington campus. The new facility will not only help develop clean power solutions, but also generate its own sustainable power.
The heavy-duty dynamometers and test cells will feature energy recovery systems to generate electricity. This will be exported to the ring main of the Cummins site, adding further capability for energy self-generation on-site. In addition, water consumption of the cooling towers will be reduced by harvesting rainwater, using a similar system already in place at the manufacturing plant.