Agco brand Massey Ferguson has unveiled a new-generation rotary combine harvester range that the company says promises a major step forward in performance and productivity for business-orientated farmers. Among a host of new features, models in the IDEAL line-up offer the biggest integral grain-tank capacity now available on the European market, the fastest unloading rate and the largest threshing area – all focused on delivering significant gains in efficiency and output.
The new machine, which will also be available from Agco’s Challenger and Fendt brands, has already been named as a recipient of an Agritechnica 2017 Silver Innovation Award.
“Built at AGCO’s European Harvesting Centre of Excellence at Breganze, Italy, the IDEAL range signals a radical new direction for our combine development,” Massey Ferguson’s Adam Sherriff said. “Utilising the full force of parent company Agco’s global resources, this is the biggest new harvesting product development project we have ever undertaken.
“It included production of 45 prototypes and six years of continuous lab and global field tests measuring performance in all crops and conditions. Everything about the machines is new – new design, new engineering, new features, new styling, even a brand-new livery in stunning graphite. Added to this, the 647hp IDEAL 9 represents a totally new market segment for Massey Ferguson.
“The impetus behind the R&D programme, which was based on our extensive Voice-of-the-Customer surveys, was to ensure that we created real business benefits for combine owners and operators, making a positive contribution to their profitability. Our focus was on fully addressing their key concerns in areas such as fuel-efficiency, performance, serviceability, ease-of-repair, grain quality, residue management, transport width, data management, hillside working and soil compaction.
“Underpinned by Massey Ferguson’s design principles of efficiency, ease-of-use, simplicity and no-nonsense dependability, our IDEAL from Massey Ferguson Combines offer major benefits in all these areas and more.”
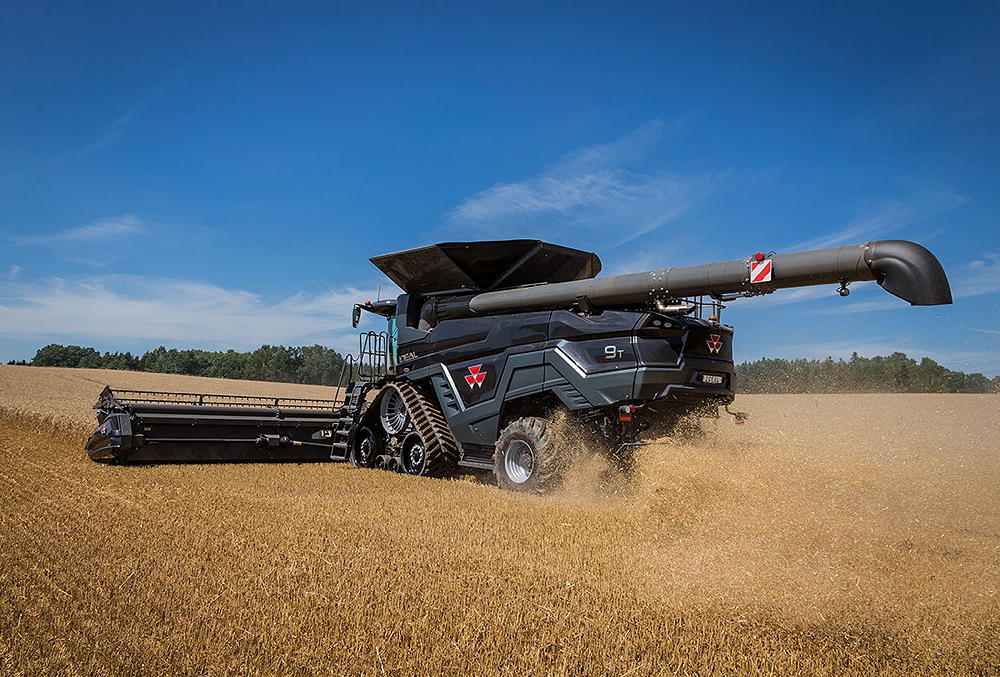
The multitude of business benefits designed into the new IDEAL from Massey Ferguson Combines include, for example, a focus on improved fuel efficiency.
“In this area, we have concentrated on ensuring that all the combine’s features make low demands on power,” Mr Sherriff said. “We have designed simple drives and incorporated a low belt count – just 13 in all. The Dual Helix threshing system uses low-pressure rotors that are designed to allow maximum space around each rotor for the straw to expand and release grain. The length of travel and the fact that the straw falls by gravity directly into the chopper really keeps the power requirement to a minimum. The length of the rotor and the extensive 1.66 square metre threshing area also allows high outputs with low grain loss.”
Grain quality benefits from the IDEAL’s low compression and extra-long rotors, which are gentle on straw, thus avoiding contamination of the sample. With the IDEALbalance under-rotor pans making pre-separation longer, they ease the job of the sieve box and fan to create a clean grain sample at high output. In addition, within the tank and unloader system, despite having the fastest unloading auger in the business, the flight pitch is designed to minimise damage to grain while optimising flow. All these features come together to make the final product as clean and as high quality as possible leading to less grain processing and helping to achieve better prices.
One of the key aspects in the design of the IDEAL combine is that it should be easy to use. A good demonstration of this is the IDEALharvest self-adjusting function option. Using 52 MADS sensors around the combine, a very simple dashboard can be brought up on the Tech Touch Terminal or the SmartConnect app on a smart device that allows the operator to choose a combination of quality, performance and sample cleanliness for his harvest. The machine itself will then fine-tune the rotor speed, fan speed and sieve opening to create the ideal settings for his choice of parameters. Uniquely, this function can provide a visualisation on the terminal or the app of the crop flow within the machine so the operator can see for himself the distribution of crop inside the combine.
For operation on slopes, the IDEAL combines are fitted with the unique IDEALbalance system. The combination of the two shaped under-rotor pans is insensitive to slopes up to 15 per cent and places the grain mix in exactly the right position for the separation pan, sieve box and fan to produce a clean sample at high output. For those on steeper terrain, a ParaLevel version of each combine model can compensate further on slopes up to 15 per cent. These models are equipped with the Streamer 140 unloader at 140 lit/sec and a 12,500-litre grain tank. The renowned ParaLevel system moves the front axles naturally and smoothly, following the ground contours and keeping the major components level.
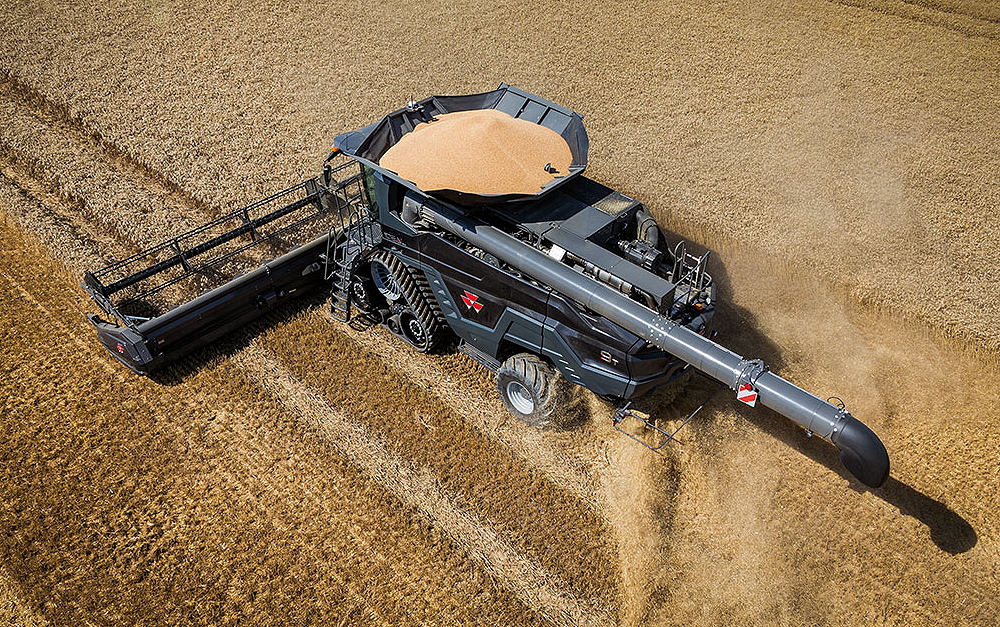
In terms of residue management, the IDEAL combine makes it easy to incorporate chopped straw as the material is able to be spread more evenly over a wider area. This is thanks to the fact that distribution of material from the ShortCut chopper can match the full width of the header up to 12m using the unique, low-power-requirement ActiveSpread feature.
For Data Management, the IDEAL Series boasts straightforward access to data and high connectivity via Bluetooth wireless technology and the AgCommand telemetry-based machine management tool. In a seamless transfer, both performance and harvest data can be fed back to the farm office, MF Dealer or the manufacturer for analysis and optimisation of operations. All levels of MF Auto-Guide steering technology are available and easily managed from the new Vision cab controls.
Soil compaction from in-field traffic is reduced as a result of the IDEAL’s large grain-tank and super-fast 210 lit/sec unloading rate option that shortens unloading cycles. Smart grain-gate operation automatically allows easy start-up for the unloader system, but can also be manually controlled to give a variable rate for topping-off trailers.
A completely new suspended track system called TrakRide has been designed for the IDEAL by Agco’s track competence centre. TrakRide is available with varying widths to suit different operations and conditions, offering maximum comfort for the operator and making a significant contribution to minimising soil compaction.
The MF armrest in the brand-new combine’s Vision cab will be familiar, but closer inspection reveals that much has changed in the operator’s area. New additions that make it even more comfortable for the driver include a new ventilated seat, a fridge unit, extra storage, new information dashboard and the ability to move the Tech Touch terminal 90 degrees to the operator’s right, which further enhances visibility of the table. Many of the operator tasks now have short cuts to make the machine easier to operate. LED lights and a camera package improve night visibility for long hours’ working.
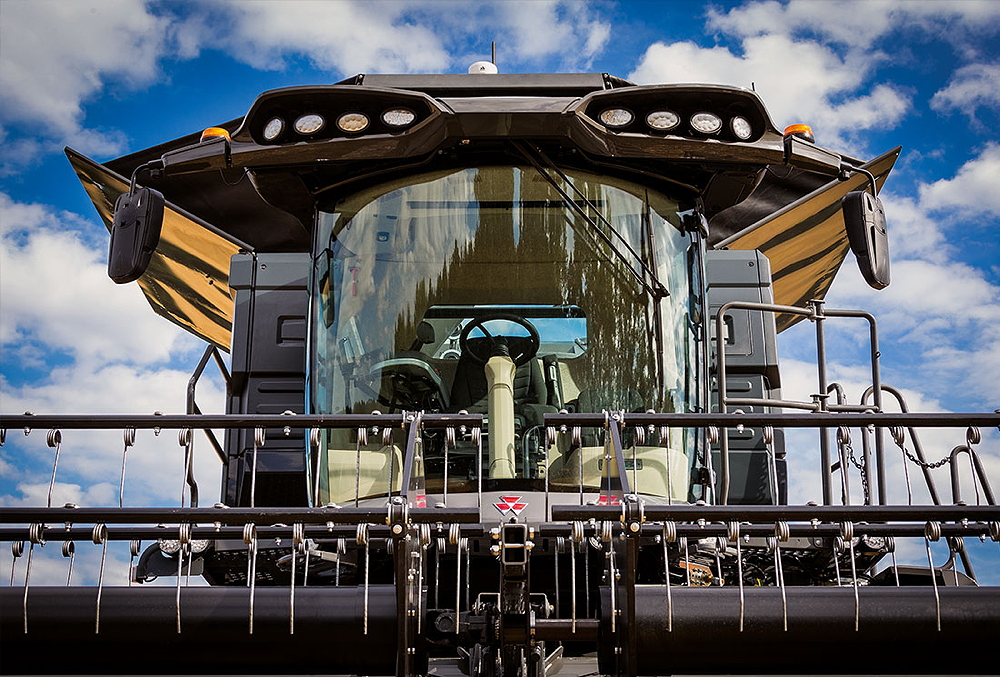
In a further feature for ease of operation, the unique new AutoDock table hook-up option saves time, promotes safety and minimises effort for the operator. When hooking-up the header from a table trailer or from the ground, the operator simply presses a button in the cab and all the connections – mechanical, electrical and hydraulic – are made automatically by a robotised process. The operator remains in the clean, safe cab and is ready to go.
The new IDEAL combines were born from an exhaustive six-year product development programme.
“We went back to the drawing board and took a fresh look at every single aspect of the combine’s architecture,” Adam Sherriff said. “This was our chance to do something totally different, push back boundaries and break the mould. It was a truly global effort harnessing the expertise and specialist knowledge of Agco’s design, engineering, manufacturing, quality, purchasing, parts, service and product marketing teams.”
A fundamental part of the project was a series of in-depth, one-to-one Voice-of-the-Customer interviews on-site with 60 combine owners and operators in 12 countries. In Europe, this included France, Germany, UK and Poland. This was followed by a mass customer survey eliciting more than 500 responses. From here, a list of critical areas for action was developed.
While customer priorities varied depending on their region and market segment, the main messages stayed the same. Key feedback from the field highlighted the need for reliability, ease of repair/parts availability, intuitive and convenient controls, efficiency and the ability of the machine to fit the customer’s operational profile.
The IDEAL combines are built at the Agco Breganze manufacturing site in northern Italy. The 25ha site has been the subject of major investment over recent years. Certified to ISO standards, some of the latest developments at the 65,000 square metre plant have seen a complete reorganisation of the supply chain and production process, the installation of new rolling and panelling machines, robot welding automated systems, a state-of-the art paint-shop and the opening of the magnificent AgriDome Visitors Centre.
A limited release of IDEAL from Massey Ferguson Combines is scheduled for 2018, with full roll-out in 2019.
For more information visit: www.masseyferguson.co.uk.