With the new Impress round baler, Pöttinger not only turns conventional baler wisdom upside down, it also sets a new standard in baler technology. Precision multiplied by performance equals impressive working results. That’s the key formula for the new Pöttinger Impress round baler, that will be available as a fixed-chamber and variable-chamber round baler and in combination with a bale wrapper.
Pöttinger’s entry into the baler market was driven by the wish to make existing technology even better. After all, many Pöttinger employees are farmers themselves. They’re continually thinking about how the machinery they work with themselves could be made better, more powerful, more convenient and safer. That’s why Pöttinger is keen to assess things from the ground up.
Where thinking outside the box isn’t enough, sometimes you have to turn everything upside down: just like the LiftUp rotor on the new Impress round balers. The rotor conveys the forage from the floating pick-up and feeds it from the front upwards into the chopping system. The crop therefore passes over the rotor and not under the rotor as on conventional balers.
Turning the crop flow literally upside down has several positive advantages. First, LiftUp technology enables a natural flow of crop, so that the forage enters the bale chamber tangentially (at an ideal angle). The result is a high intake capacity that translates into high baling performance with very low disintegration losses.
In addition, the bale chamber is fed more uniformly across the whole width, that greatly reduces any left/right steering correction needed to produce perfectly shaped bales. And, the bale always starts to form reliably in any situation. Quite simply; it’s always ready. Regardless of whether in wet or dry conditions, whether for straw, hay or silage – here’s one machine for all operating situations.
Second, the Flexcut 32 short-chop system on the Impress with up to 32 knives and proven individual knife protection system ensures the very best forage quality. With silage, the uniformly short chopped length ensures a homogenous structure that requires less intensive mixing when using feed mixing wagons. This has a positive effect on the fermentation stability and, as a result, on the quality of the forage. When used for straw, short chopped straw for adding to feed and for bedding can be produced for a minimal extra power requirement.
Pöttinger, the world leader in loader wagons, has thus managed to integrate loader wagon chop quality into a round baler for the first time. Short chop not just for silage, but also for hay and straw; that’s unique on the market. Another innovation is the use of TwinBlade reversible knives, that provide double the service life.
Third, the Impress features a swing-out chopping system with the proven Easy Move pull-out knife bank. The highest level of convenience is ensured with maintenance taking place at workbench height outside the bale chamber. The higher the number of knives, the more important the ease of maintenance. The Pöttinger Impress provides an ingenious and convenient solution.
Technical highlights
The five-row, controlled floating pick-up is 2.3m wide and is equipped with a wind guard with swath roller and transfer bars as well as two cross conveyor augers. The floating function with 120mm of vertical travel measured at the tines guarantees excellent ground tracking and best raking quality for the cleanest crop take-up.
The new, pull-out FlexCut 32 short chop system features 32 TwinBlade reversible knives with the NonStop individual knife protection system to provide a theoretical chopped length of 36mm across the entire width. The shorter chop length enables higher compression of the crop and thus higher bale density with all harvest material (silage, hay, straw). This brings about a reduction in transport costs as well as storage costs because smaller storage space and less handling are required.
In addition, with silage, the uniformly short chopped length ensures homogenous mixing of the forage. This has a positive effect on the fermentation stability. Less power is needed for the mixer wagon and the bales are easier to break up. Livestock leave behind fewer long stalks of forage when straw has been added to maize or grass silage.
Thanks to the theoretical chopped length of 36mm, with straw it’s no longer necessary to purchase a cost intensive pre-baling chopper or post-baling shredding system. The combination of LiftUp rotor and pull-out EasyMove chopping system provides a unique level of maintenance friendliness: ergonomic maintenance while standing outside the danger area of the round baler.
Assisted by the patented knife group switching system, the desired number of knives to be used can be selected flexibly. No dummy knives are required because the knives that are not in use cover the knife slots and the gaps between the knives.
Add all these facts and advantages together and the range of applications of a Pöttinger Impress round baler is much wider than a conventional round baler.
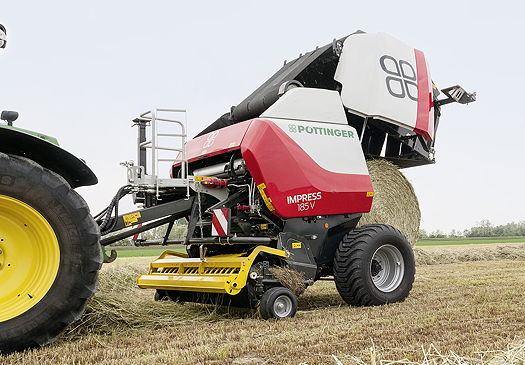
LiftUp rotor
The overhead LiftUp rotor, with its patented spiral configuration of tines, feeds the crop into the bale chamber tangentially in a wide blanket. This method promotes a flow that conserves the crop with very low disintegration losses. Any material that does fall through is fed back into the flow by the patented cleaning rotor. This is a unique design that solves the problem of disintegration with a higher number of knives.
If a blockage occurs, the cross section of the duct can be increased temporarily on the Impress by lowering the patented vertical-travel chopping system floor. This allows the blockage to clear easily and effortlessly.
Reliability of round balers in all operating conditions – regardless of whether you are baling silage, hay or straw – has always been a key issue. Pöttinger focused intensively on reliability during the development of the new Impress: tangential crop flow into the bale chamber, optimised bale starting volume, and two patented lower starter rollers on the variable baler to ensure a reliable start to the bale with all 32 knives in action in all operating conditions. This level of reliability in combination with a short-chop system was previously not available on the market, especially when baling straw.
Bale chamber
The bale chamber has two aggressive starter rollers above and below to make sure the bale is formed reliably in every situation. The bale chamber is designed for the highest possible baling compression to offer the greatest productivity.
The variable chamber baler is equipped with three endless belts. The baling pressure is adjustable in three zones (soft core setting) to ideally adapt to individual requirements. A pivoting chopping system floor enables variable intake volumes for hay. The tailgate interlocks hydraulically.
The fixed chamber baler has large self-aligning bearings (50mm diameter) and has two different compression rollers to the front and rear to ensure reliable rotation in every operating situation – even with straw.
The integrated net binding system also boasts several special features. Using a feeder plate, the netting is fed reliably into the bale chamber. The netting is propelled into the bale chamber in good time. If binding is not successful first time, up to three further attempts are made. The netting knife actuates automatically. Netting up to 1.3m wide can be used.
Model overview
The Impress will be available both as a fixed-chamber round baler and a variable-chamber round baler, as well as in combination with a bale wrapper, each as a Master or Pro version. The Master version features a double-acting spool valve offering pre-select functions for the pick-up, chopping system floor and number of knives as well as a second spool valve for the tailgate. The Pro version allows all functions to be controlled directly from the operator terminal (Power Control or Isobus). This version provides an automatic function sequence and all functions can be actuated directly.
The balers are available with tandem axles up to 500/50-17 or single axles up to 500/60R22.5, while the baler/wrapper combinations are supplied as standard with tandem axles up to 500/50-17, or with 500/60R22.5 in tandem as an option.
The complete production of models for 2016 has already been sold out, but wider market introduction is planned for 2017.
For more information visit: www.poettinger.at.